Automakers are putting their engineering and fabrication skills to use in the fight against COVID-19 as they can, it seems. Some, like Tesla, are re-purposing existing parts to help patients and medical providers. Others, like Lamborghini, are using their team of upholsterers to work making masks and protective face shields. Ford, which showed off an early sketch of a possible powered respirator early in the fight against COVID-19, has also joined the fight, producing face masks and face shields, of course, but it’s the company’s latest hack that may end up being the most significant. It is now making reusable gowns from airbag materials.
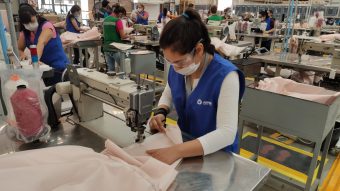
“This was a really great find,” Ford director Marcy Fisher says, as she explains how the lightweight fabric used in airbag construction — a material called Nylon 6,6 — is perfectly fluid-resistant. What’s more, this fabric that’s used in parachutes, carpets, and garden hoses is not only ideal for PPE — it’s also washable. “The gowns are washable and they retained their performance qualities, (even) after 50 times in the wash.”
Ford didn’t come to this realization alone, of course. In an interview with Quartz magazine, Ford explained that it has been working with local hospitals to “finesse” the sewing pattern for the isolation gowns and have conducted internal tests to make sure the reusable gowns are meeting the standards set by both the American Society for Testing and Materials (ASTM F3352-19) and the Association for the Advancement of Medical Instrumentation (ANSI-AAMI PB70-2012).
It’s not just a sturdy smock, in other words. It’s a well-engineered piece of medical equipment that is critically needed to help keep healthcare workers safe as they fight the Coronavirus pandemic.
Ford, for its part, is proud of the work it’s doing these days. “We knew that to play our part helping combat Coronavirus, we had to go like Hell and join forces with experts like 3M to expand production of urgently needed medical equipment and supplies,” said Jim Baumbick, vice president, Ford Enterprise Product Line Management. “In just three weeks … we’ve unleashed our world-class manufacturing, purchasing and design talent to ‘get scrappy’ and start making personal protection equipment and help increase the availability and production of ventilators.”
Oh, and that sketch of a powered respirator that was set to be made from Ford HVAC controls and seat fans? The one we mentioned in the first paragraph? That one’s also in production. They have capacity to build about 100,000 of them with a staff of UAW volunteers, and they look absolutely awesome.
Author: Jo Borrás
Source: Clean Technica