Having heard that one company was established in 1828 and that 85 per cent of their products are exported worldwide, these are the credible facts. The company we talk about is Witkowitz, the famous Czech corporation, which apart from inheriting almost two centuries long tradition, has a new look. One of the companies it includes that today holds a name of Witkowitz ENVI delivers its products to dynamically developing markets related to the protection of water resource and other environmental projects. Their production program base consists of large capacity tanks made of enamelled, stainless and comaxite* sheets. The experienced team is responsible for design, manufacture, installation and maintenance of wastewater treatment plants (WWTP), biogas station and liquid fertilizer warehouses, as technological units based on their tanks.
Although metalwork is a legacy of the parent company, the comeback to the industrial scene has occurred with the intense development of technology in the second half of 20th century, which had resulted in changes in all spheres of life. However, those changes haven’t brought only well being, but they left huge vestige when it comes to pollution in nature, lack of drinking water and an enormous increase in waste quantity. Meanwhile, the need for energy, especially for the quality and clean one, has been multiplied. As a response to these demands, being imposed by a different strategical development, the production programme was made, and Witkowitz ENVI covers it from 1966 when they became a new member of the company. Enamelled tanks from this factory have become a synonym for success and base for gradual adoption of present-day technological solutions in fields of wastewater treatment, storing biological waste and manure, and eventually in the field of biogas production and electricity generation. With Vladimir Sitta, the general manager and chairman of the Witkowitz ENVI A.S. Board, we talked about the technological solutions made by this company.
EP: On account of a rather long history in the field of metallurgy, and because of modern-day demands for environmental protection, you established the production of tanks made of enamelled sheets which for decades have been the strategic product. What is their scope of us and what industry are they mostly used in?
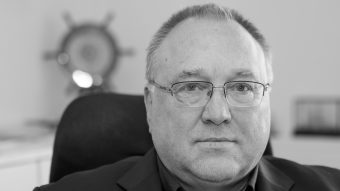
Vladimir Sitta: Sheets enamelling is done at the temperatures above 800 °C, where the surface of the steel is covered with a double layer of melted glass. The long-lasting protection of the surface of the steel is achieved this way, and enamelled tanks hold water just as drinking glass does. When it comes to quality, this is the unexcelled way of storing water and many other aggressive fluids and materials. That is the exact thing that ensured the good place of enamelled sheets at the market.
We have been into this business for more than 50 years, so it is no wonder that more than 10.000 tanks with our old and new logos can be seen throughout the world. Above-ground tanks covered with glass have the broadspectrum usage and can be applied in agriculture, industry, water management and energy sector. Our tanks and silos can contain liquid and bulk materials. High variability of design enables simple fitting of additional equipment into a currently wide-spread, above mentioned technology units. Aside from storing drinking and wastewater, sludge and rainwater, the tanks are designed to hold body fluids from cattle, pigs, and various industrial water, for suspension, silage, haylage etc. They are suitable for storing lime, cement, ash, biomass, gravel, salt, soot and other materials.
EP: What companies already use the Witkowitz above-ground tanks in Europe and the world?
Vladimir Sitta: We make deliveries directly to end buyers too. Still, the majority of plants are built as a result of longterm cooperation with the multinational companies which try to solve problems with drinking water shortage or wastewater treatment in all continents. Some of our clients are VEOLIA, SUEZ, SYMBIONA, AES Arabia, AQUARIUS, Tank Team, Gruppo Asham, Nijhuis Ind, Monostore, Agrofert, Hydrotech etc. On our web site, there is an interactive map where thousands of locations can be found where those projects were implemented. Also, visitors may see at our web site photo-documentation for certain facilities. A few hundred of water tanks were installed only in Arab states. However, a great number of them were implemented in Mexico, Malesia, north Africa, China, Spain, Poland, Russia, France, Bulgaria and Croatia. So, you can find our tanks from Vladivostok to Chile. Precisely in the Chilean town of Osorno is where our most distant reference is situated. This place and the Witkowitz region, where our production is located, are 13,407 km apart from each other.
EP: What is the most significant comparative advantage of your products in relation to the existing offer at the market?
Vladimir Sitta: The construction of the tank is made of prefabricated elements, which ensures very fast assembling, and along with that, an optimal time for completing the whole project. Transportation of disassembled tank is very easy and simple since all is packed in pallets and containers. It takes a rather small surface for building a tank, which generally consists of a belt 1.5 m wide around the tank. In comparison to a concrete tank, those we make have a small weight. Also, it is easy to inspect the tank after installation and during testing. Machinery isn’t required to build these tanks. Just a forklift or crane is needed. Occasionally, there is a necessity of crane for installing special roof. Mounting is done by using our technology for lifting from the foundation, which means that works are carried through from a ground level and having avoided almost entirely operations at altitude. That diminishes the risk of injuries at the construction site. The tank design can be adjusted to the installation of technological equipment such as pumps, mixers etc. The tank modification, reassembling due to breakdown or relocation is done very quickly. It is also uncomplicated to repair the damaged tank parts, and it is quick and cheap to disassemble the tank. After the expiry date, the tank can be recycled – material can be sold as a steel waste, unlike concrete which remains as a ruin. We have a lot of experience with tank installation throughout the world and in various extreme conditions. The fusion of glass and steel is achieved by their melting at high temperatures, which makes these tanks very durable. The planned operating life of the tank is at least 30 years, and some of them were in use for more than 40 years. Tanks are highly resistant so suitable for storage of even very aggressive substances, in comparison to concrete or tanks made of plasticized steel sheets. Enamelled steel tanks are resistant even in extreme marine conditions. Enamel is resistant to most bases, acids and organic solvents, and it stays unaffected by substances from different emissions. They can be used for all the contents with 3-12 pH value. There is no need for the repainting of the tank. The surface is impervious to all abrasive materials with hardness less than 6 or 7 (glass is 7). It is not possible to scratch the surface with a metal object (knife or other tool steel), and unwanted graffiti and spray paints are easily removed from enamelled surface too.
In focus:
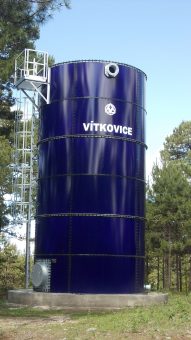
EP: Since these enamelled tans can hold drinking and seawater, and different kind of wastewater too, it isn’t unusual that your offer contains also wastewater treatment plants. What are the biggest benefits of this technology?
Vladimir Sitta: Since we established the production of enamelled tanks, the development of society and increase in need of wastewater treatment plants have led to massive construction of wastewater treatment plants near the cities. We were developing our systems for water treatment for years, such as Hydrovit, but today the WWTP design is always adjusted to the client’s needs. We have our design team and installers for fieldwork. The base of the WWTP used to be triple (or double) biological tank which consisted of enamelled sheet tanks placed concentrically: sludge tank, tank for activation and tank for deposition. Tank for activation was technologically used in the process of pre-denitrification (D-N) or sludge regeneration (R-D-N), as process variations during nitrogen removal. Computer-controlled aeration was used for air ventilation of the tank. It is the finest bubbles aeration which ensures high efficiency and low working costs. The new millennium has brought new rules. Design now follows investors’ demands and local needs for technology, and to the extent imposed by production processes and available materials. Aside for above mentioned, plants can have line production and multi-lines production, and they can not only provide water treatment but they also frequently include sludge to energy treatment.
EP: What happens to sludge which remains as a by-product after treatment?
Vladimir Sitta: Sludge coming from WWTP is today’s topical issue. Sludge treatment options depend on relevant national regulations. There has been a tendency in the European Union for the past few years to tightening of regulations concerning sludge treatment. In the Czech Republic, typically in WWTP for up to 50.000 EO sludge that is formed in deposition chamber (in front of WWTP) and excess of sludge from secondary depository are taken to the reservoir where they get mixed and stabilized so that free biological decomposition can be prevented. A solid and fluid fraction is separated, a watery element is returned to the treatment process, whereas the solid part after being sanitized and condensed is scattered in fields as manure. Also, sludges from big WWTPs (above 50.000 PE) after being processed are taken to landfills. In the past few years, there has been an increase in the number of sludge incineration plants (for sludge drying, firing, etc.). After being dried and processed, a mass can be added then as an aggregate to concrete (in the form of granules), can be used as fuel in cement plants and blast furnaces, or added as manure (after being grounded). Sludge is always processed or disposed of according to existing regulations, and it is logic to further optimize its treatment process to reduce the costs. In the EU there are several different norms and solutions. Many countries in the EU are committed to removing hard metals and antibiotics from sludge, while a lot of countries have the obligation to incinerate sludge completely. Criteria will be even tighter!
Interview by: Tamara Zjacic
Read the whole Interview in the new issue of the Energy portal Magazine NATURAL RESOURCES, march – may, 2020