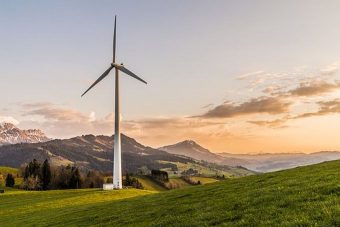
Constructing offshore wind turbines in port rather than onsite in variable conditions has been found to be the most cost-effective method, according to research published this week by researchers from the University of Delaware.
Researchers from the University of Delaware, who worked closely with offshore wind industry partners, have developed a new method for constructing offshore wind farms that they believe is cheaper, faster, and which could increase the scale and pace of offshore wind deployment that would match the region’s scheduled retirements of nuclear and coal-fired power plants.
Specifically, the University of Delaware researchers concluded that their new construction process would save up to $1.6 billion per project over conventional construction methods, and take half the construction time.
The primary aspect of the research was that the entire wind turbine structure — from seafloor mounting through to the top of the wind turbine — could be assembled in one piece in port, before being transported as a single unit and in one step installed into the seafloor at its offshore site.
“In planning for offshore wind power, the big question is how we generate electricity cost-competitively, and at a scale that is both a relevant replacement for aging power plants and also applicable to climate change,” said the project’s principal investigator, Willett Kempton, professor in the College of Earth, Ocean, and Environment (CEOE). “We’re the first people who have shown the engineering details, step-by-step, how to achieve that.”
For anyone who knows anything about offshore wind construction, this might sound outlandish, but the researchers have found that this can be done with current technology.
Further, the University of Delaware researchers based their modeling on a 10 MW (megawatt) wind turbine with support structures, weighing in at 2,500 metric tonnes. The research therefore focused on how to build and move these massive constructions within port.
“Instead of today’s method, carrying out parts separately and individually assembling each in the ocean, we have an assembly line on shore,” Kempton said. “We spend more money in port, but we spend far less money at sea.”
Beyond the economic benefits of this research there are also non-monetary benefits such as shifting more of the assembly from sea to land, which allows for construction regardless of weather and reduces the time at sea from 3 days to 10 hours per wind turbine.
Source: cleantechnica.com