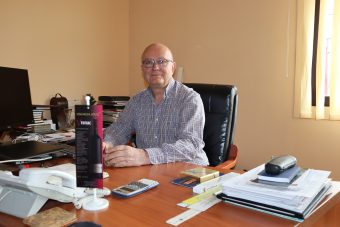
In an old wine cellar, in the middle of rolling vineyards at the bottom of the massif of Stara Planina, two brothers were thinking on how to make a course of making excellent wine from a good grape harvest more certain. It was their turn to take care of this family heritage. In little wineries, fine grapes don’t necessarily make superb wine. It was obvious that they can’t rely any more on a technique which their ancestors used to sustain the temperature in barrels in cold or warm nights. The Jovic brothers have already had substantial engineering experience, and it was pointing them to find a solution in close vicinity. At the desk in the R&D office of their own company for ventilation and heating which they founded in 1995 in Knjazevac. So that is how the Alfa Clima company has become a link between thermodynamics and winemaking.
Having implemented the temperature control process in wine fermentation, they have achieved quality, but also different wine character. It hasn’t lost its acids nor drinkability, let alone freshness of its aroma. The wines from the Jovic winery have gain distinctiveness, and the word has been spread – about their wines much as about an airto-water type cooling system with freon which the Jovics designed and installed in their Alfa Clima company. Little wineries from across Serbia have got a chance to take a turn in technology and instead of using enological chemistry, to install this device for fermentation control and cold stabilization of the wine. Thanks to this solution, almost 30 local wineries hitherto can be proud of having ”healthy”, clean wines in their offer.
Meanwhile, the brothers Sasa and Jovan Jovic have come up with the idea to design a device for quick and thorough cleaning of wine barrels and tanks. Soon the Parko unit was born in the Alfa Clima facilities. It is now indispensable in the inventory of small local cellars, which uses water vapour to efficiently clean and sterilize containers. Although it is quite obvious that twosome Jovic doesn’t lack innovation, we were curious to find out how they intend to solve the problem with Freon. Freon is the primary cooling liquid in most systems in our country, whose withdrawal is just a matter of time. We got an impression that Sasa Jovic, the general manager at Alfa Clima, couldn’t wait for someone to show up and ask this question.
“No doubt that the death knell for freon has been tolled, but there are options such as ammonium, carbon dioxide and propane. In the field of ventilation and technological processes in positive temperatures, or slightly negative, propane behaves well – and if there wasn’t for its flammability, it would be the perfect solution. Still, that is where our creativity has stood out. We have come up with a technical solution and registered a patent since we have reduced the risk of flammability and fire to a minimum. This invention, named Propsafe, was granted by the Innovation fund and currently, we are in a testing process. By the end of the year, we will have final prototypes.“
To say that propane usage in small domestic appliances isn’t a novelty is something that Sasa confirms too. However, there is no refrigerant grade propane R290 at our market, nor has been its usage regulated by law. Without this refrigerant, the whole Propsafe project could come to a dead end. The manager at Alfa Clima says that this type of fluid is imported with a permit granted by the government. Hitherto, there hasn’t been any demand, so the permits haven’t been issued. Until the problem is solved, they keep testing the prototype which is filled with Freon since that is a simpler and more available option.
“It is not only the question of importing propane, but also about handling, storing and licensing the workers who will be using it. The regulations are needed, and their lack is imposing a problem for engineers, clients and service providers. For the record, we are just now trying to license service providers for Freon usage, whereas it is slowly going out of use. The system is slow and inert, so it is important we animate it”, explains Sasa having mentioned that there is a great demand for propane chillers. “Croatian companies make bigger, purpose-built chillers with propane for Nordic market and their production is sold for a year or two in advance. Although the propane usage hasn’t been regulated there either, they overcame the problem by delivering the device that isn’t filled. In our case, that is rather complicated, since we oriented future production range towards households and low-power devices.“
Their efforts in making a request more striking to institutions are backed up by the Union of mechanical and electrical engineers and technicians of Serbia. Therefore, Sasa and Jovan are hoping that the problem of propane importing and handling too will be solved sooner. While waiting for a favourable outcome, there are no delays in the realization of other plans. Along with two production lines, which include heat pumps as standard devices for ventilation and with a range of purpose-built devices, Alfa Clima is today a heartbeat away from introducing the mass production of standard heat pumps for smaller buildings and households. Proud-hearted, Sasa points out this to be a turning point for the company as the realization of this goal leads to conquering markets which hitherto haven’t been within their reach. On their way to new clients, one of the very important steps was establishing a testing station where prototypes of devices are checked in a quick and precise manner. “When you are offering pump 300 kW, it must have the exact power, and not being able to achieve it in ideal conditions. In the testing station it is what we check precisely”, confirms Sasa.
Significant savings thanks to heat pumps
Production at this company in Knjazevac was focused from the early days on heat pumps whose main purpose was energy savings. Back then, the price of electric energy was pretty low, so only a few were considering energy savings. Sasa says in hindsight it seems unbelievable that they were able to get clients at all. ”Today, although the electric energy we use still comes at a price lower than the European average, people think that this situation at the energy market won’t last too long and wonder about the future. Therefore, clients install our air-to-water and water-to-water types of pumps, namely two basic types we have been making from the start, which are even today in demand. We are particularly proud of the fact that some of the pumps are still in use even though they were installed more than twenty years ago.”
Now they make the fourth generation of heat pumps, which means that they have implemented four considerable changes in the construction and concept of those devices. The pump’s power ranges from 5-6 kW to 500 kW. All inovative solutions have been made in their R&D office where the team of engineers assemble each time they face a production challenge. ”When it comes to pumps waterto-water, we use the energy of groundwater in wells. We have made a new design of heat pump with a different type of heat exchanger which we produce. That way we have made shorter and cheaper not only installation but also the pump. At the same time we raised the degree of heating since we don’t have the interchanger”, says the Alfa Clima manager. He emphasizes benefit not only from reducing the costs but also from better heat pump efficiency.
„Groundwaters that are not too ’aggressive’ or murky we can use directly in heat pumps. But with aggressive water which happens to be loaded with Sulphur and metal residues such as manganese or iron, we put the interchanger into the pumps. River and lake water we can also use – where in the coldest days the water temperature doesn’t exceed 1°C or the water even gets frozen. In those pumps, we utilize different exchangers, and that is a nice and appealing solution. Anyway, there is a solution to every type of water. Still, we might say that heat pump water-to-water is the most efficient”, explains Sasa adding that there is also a subtype of this pump. “The most interesting is wastewater, and the Germans are the first who started using it for generating electricity. In two buildings we installed pumps which use waste water. In the spa centre in Mladenovac we built in a system for the use of wastewater coming from showers and other sanitary ware. The pump capacity is 300 kW, and this energy is used for heating the sanitary water for the whole building, so ten times less energy is consumed in comparison with other energy sources. That way, the users can pay off the investment faster.”
Another pump was built in the Tornik hotel at the Zlatibor mountain which covers up to 36.000 m². The project also involved the construction of the separate sewage system which allowed the installation of the pump that would use waste water from sanitary wear. According to some estimates, pump repayment period in hotels can be reduced to up to one year based only on the savings of the sanitary water. Sasa says that realistic expectations are to pay off the investment in several years. “It’s a common knowledge that in hotels, no one thinks about saving hot water. Therefore, it is indispensable to plan the savings from the early stage of the project development for the hotel.”
Prepared by: Tamara Zjacic
Read the whole article in the new issue of the Energy portal Magazine on ENERGY EFFICIENCY, June 2018. – August 2019.